Ⅰ.Introduction
High-purity argon gas is a commonly used shielding gas in argon arc welding. Its high purity and inert characteristics make it an ideal choice for protecting the welding zone and ensuring high-quality welds. This article will explore the application of high-purity argon gas in welding, starting from the properties of argon gas. We will also discuss a range of issues that may arise in practical applications.
Argon (Ar) is a chemical element and belongs to the group of inert gases. It has an atomic number of 18 and a chemical symbol of Ar, placing it in the 18th group of the periodic table. Positioned between oxygen and nitrogen, argon is an inert gas that does not readily react with other substances. This inert nature enables it to effectively protect the welding zone by preventing the entry of oxygen and moisture, reducing the risk of metal oxidation and corrosion. Argon has a melting point of -189.2°C and a thermal conductivity of 0.0175 W/(m·K). During welding, it provides sufficient heat to rapidly melt the metal and form stable welds. Argon is the third most abundant component in the Earth’s atmosphere, accounting for 0.934% of its volume. It is relatively easily obtainable and can be purified to high purity through air separation units, significantly reducing the cost of raw materials for businesses.
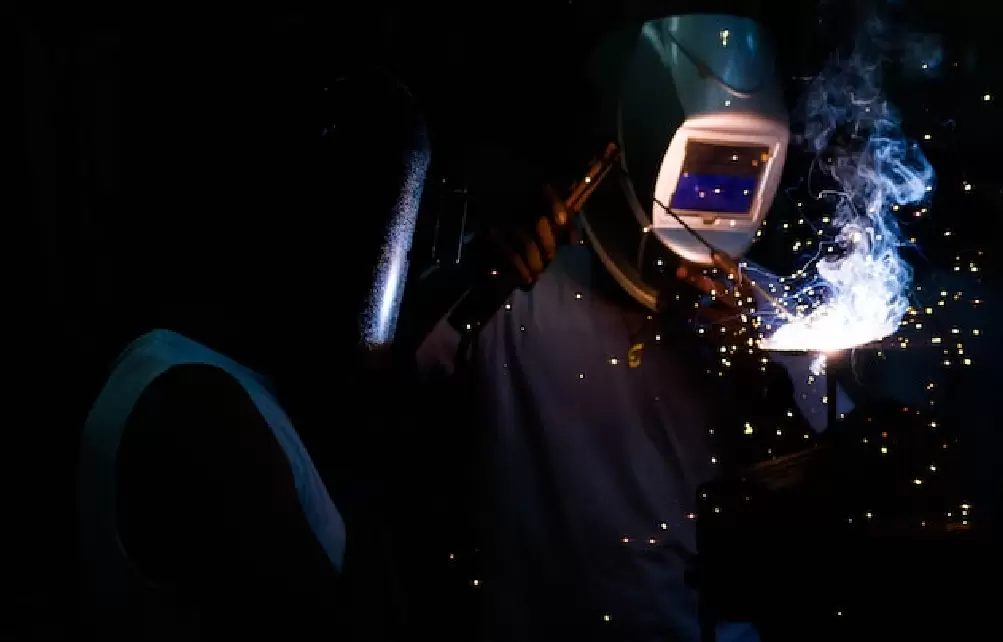
Ⅱ.Argon arc welding technology
TIG welding (Tungsten Inert Gas Welding), also known as Gas Tungsten Arc Welding (GTAW), is a commonly used metal welding technique. It utilizes an inert gas, typically argon, to protect the welding zone and maintain the quality and purity of the weld.
1. Working Principle of Argon Arc Welding:
Argon arc welding primarily consists of two components: the tungsten electrode and the shielding gas. During the process of argon arc welding, the welder uses a tungsten electrode to create an arc in the welding zone. The tungsten electrode has a high melting point and excellent electrical conductivity, allowing it to withstand high temperatures and maintain arc stability. Simultaneously, the welder uses a handheld filler material to add metal to the weld joint. Argon gas is the most commonly used shielding gas and is often mixed with helium. The role of the shielding gas is to prevent the reaction between the welding zone and oxygen and moisture in the air. Argon gas possesses inert and stable characteristics, which help maintain the purity of the welding zone and prevent oxidation and corrosion of the metal. The shielding gas is expelled from the nozzle of the welding torch, forming a protective layer that surrounds the arc and the welding zone.
2. Argon Gas Requirements:
In argon arc welding, argon gas is used as the shielding gas, and it requires relatively high purity. Argon gas with lower purity levels may contain impurities such as oxygen, nitrogen, and moisture. These impurities can have adverse effects on the welding process and weld quality. However, the use of high-purity argon gas ensures the purity of the welding zone and reduces the risks of oxidation and contamination. Argon arc welding is commonly employed in applications that demand high-quality and visually appealing welds, such as aerospace, food industry, and pharmaceuticals. High-purity argon gas provides better welding protection, resulting in cleaner, more uniform welds with enhanced aesthetics. Argon gas with lower purity levels may lead to issues such as oxidation, corrosion, or other undesirable effects in the weld joint. Additionally, some special materials have higher requirements for argon gas purity. For instance, stainless steel welding is more sensitive to the purity of the shielding gas, necessitating the use of high-purity argon gas to avoid corrosion or contamination in the weld joint.
Ⅲ. Advantages of Argon Arc Welding
1. Argon arc welding can produce high-quality, defect-free welds. Due to the protective nature of argon gas, the welding zone is shielded from contamination and oxidation present in the external atmosphere. The protective atmosphere formed during the welding process prevents oxidation, corrosion, and the infiltration of impurities into the weld, resulting in uniform, sound, and mechanically robust welds.
2. Argon arc welding provides precise heat control in the welding zone. Due to the high thermal conductivity of argon gas at high temperatures, the welding zone can rapidly melt and cool. Welders can control the heat input by adjusting parameters such as arc current, voltage, and argon gas flow rate, allowing for precise control over the welding process.
3. Argon arc welding excels in the welding of thin materials. Due to the relatively low heat input, it helps to avoid issues such as excessive heating and deformation. Welders can achieve high-quality welds on thin materials by fine-tuning welding parameters, meeting the requirements for welding thin-gauge components.
Ⅳ. Challenges and Issues
Although high-purity argon gas offers numerous advantages in welding, there are also some challenges and issues to consider, such as gas leakage, environmental impact, and supply chain issues.
1). Compared to regular purity argon gas, the production and handling processes for high-purity argon gas are more complex. While the cost of obtaining high-purity argon gas may be lower, achieving high purity requires precise gas separation and purification techniques, involving large-scale gas production equipment and specialized technical operations. For projects with significant gas consumption, the production of high-purity argon gas may significantly increase welding costs. Therefore, if on-site gas production is not required, it may be more practical to purchase high-purity argon gas from professional gas companies.
2). For large-scale or long-duration welding projects, a stable supply of high-purity argon gas is crucial. However, the stability of argon gas supply may be subject to limitations in the supply chain, such as insufficient availability, logistical issues, or technical malfunctions. Unstable supply can result in interruptions, delays, or welding quality issues during the welding process. It is recommended to choose a reliable and stable gas supply chain. JinHong Gas specializes in the supply of various high-purity specialty gases, offering both cylinder and tank supply modes. With a professional supply team, JinHong Gas ensures high-quality service throughout the process, reducing your gas consumption costs.
3). Due to the higher purity of high-purity argon gas, it is more prone to leakage during storage and transportation. Gas leakage can pose safety hazards and result in wastage of argon gas. Leaked argon gas increases the frequency of cylinder replenishment and may pose potential risks to the surrounding environment and personnel. It is essential to implement proper storage, handling, and safety measures to minimize the occurrence of gas leakage and ensure the efficient utilization of high-purity argon gas. Regular inspections, maintenance of gas storage facilities, and adherence to safety protocols are crucial in mitigating the risks associated with gas leakage.
It is important to note that these issues are not inherent problems with high-purity argon gas itself but rather specific requirements and usage environment related to its application in argon arc welding. Through proper management and operation, these issues can be minimized, ensuring the safe and effective use of high-purity argon gas in argon arc welding. Implementing appropriate safety protocols, regular equipment maintenance, and proper training for personnel handling the gas are crucial to mitigate potential issues and ensure the optimal performance of high-purity argon gas in welding applications.
Ⅴ.Conclusion
High-purity argon gas plays a significant role in argon arc welding, offering inert characteristics and excellent thermal conductivity, resulting in high-quality welds with aesthetic appeal. However, the use of high-purity argon gas in argon arc welding also presents challenges such as cost, gas leakage, and environmental concerns. Some of these challenges can be addressed through technological improvements and management measures, while others may be more difficult to resolve. When utilizing argon arc welding technology, it is important to weigh its advantages and challenges, select a reliable gas supply partner, and implement appropriate measures to ensure welding quality, safety, and environmental sustainability.