Comparison Table: Common Welding Techniques
Welding Method | Shielding Method | Operation Style | Suitable Materials | Advantages | Disadvantages |
---|---|---|---|---|---|
Stick Welding (MMA) | Flux-coated electrode | One-handed (manual) | Steel, stainless steel, cast iron, etc. | Portable, low equipment cost, wind-resistant | Labor-intensive, high fumes, needs slag removal |
TIG Welding | Inert gas (Argon) | Two-handed (torch + filler) | Aluminum, copper, stainless steel, alloys | High precision, clean welds, ideal for thin or exotic metals | Requires high skill, slower speed, sensitive to conditions |
MIG Welding (CO₂) | CO₂ shielding gas | One-handed (semi-automatic) | Carbon steel, low-alloy steel | Easy to learn, high efficiency, good visibility | Prone to spatter, not wind-resistant, needs gas cylinders |
Submerged Arc (SAW) | Flux powder covers arc | Automated/Semi-automated | Thick plates, large components | High deposition rate, deep penetration, low fumes | Limited to flat/horizontal welds, large equipment required |
Stick Welding (Manual Metal Arc Welding, MMA)
Stick welding creates an arc between a coated electrode (welding rod) and the workpiece. The intense heat melts the rod and the base metal, forming a weld. The rod’s flux coating melts during welding, creating a gas shield and slag to protect the weld pool from oxidation. This method requires only one hand to operate and is highly portable, making it suitable for outdoor and small-batch work. However, it generates significant fumes and requires slag removal after welding.
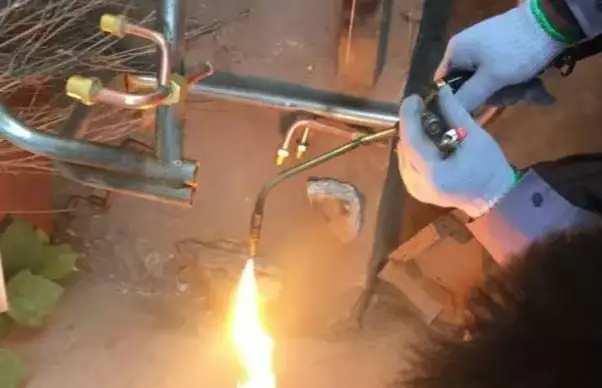
TIG Welding (Tungsten Inert Gas)
TIG welding uses an inert gas, typically argon, to shield the weld area from atmospheric contamination. It involves holding the torch in one hand and feeding a separate filler rod with the other, making it a two-handed operation. This method is ideal for welding non-ferrous metals like aluminum, copper, and stainless steel. It produces precise, high-quality welds but demands more skill and coordination.
MIG Welding (Metal Inert Gas, also known as CO₂ Shielded Welding)
MIG welding uses a continuous wire electrode fed through a welding gun and a shielding gas, commonly CO₂. It is widely used for welding carbon steel and suitable for both automated and all-position welding in indoor environments. MIG welding has higher efficiency and cleaner welds than stick welding but requires gas cylinders and produces more spatter. It lacks wind resistance, making it less ideal for outdoor jobs unless wind protection is provided.
Submerged Arc Welding (SAW)
In SAW, the electrode and granular flux are separate. During welding, the arc is submerged under the flux, which prevents oxidation and reduces visible arc light. It is mainly used for large-scale components, offering high deposition rates and deep penetration. This process is generally automated or semi-automated and suitable for heavy industrial applications.
Welding Rods and Their Composition
Welding rods consist of a metal core (weld wire) and an external flux coating. The core is typically made from high-grade steel. The flux coating contains materials like marble, fluorite, water glass, ilmenite, and organic compounds. When heated, these components decompose to form protective gases such as manganese oxides, hydrogen fluoride, and nitrogen oxides. However, prolonged exposure to welding fumes can lead to serious occupational hazards like pneumoconiosis.
Pros and Cons: MIG vs. Stick Welding
MIG Welding
MIG, or CO₂ gas shielded welding, is widely used in structural steel projects involving low-carbon and high-strength low-alloy steels. It supports semi-automatic and automatic all-position welding and is well-suited for indoor environments.
Advantages:
- Easy to automate and ideal for high-efficiency production
- Uses bare wire, offering concentrated heat input and a small heat-affected zone
- Produces clean welds with minimal distortion
- Lower overall costs—approximately half that of stick or submerged arc welding
Disadvantages:
- Significant spatter, especially if parameters are not well-tuned
- Not suitable for metals prone to oxidation
- Requires shielding from wind in outdoor or open-air settings
Stick Welding
Stick welding can be used on most metals, including carbon steel, alloy steel, stainless steel, heat-resistant steel, low-temperature steel, cast iron, copper, and nickel alloys. It also supports dissimilar metal welding and repair jobs.
Advantages:
- Portable and requires minimal equipment
- No shielding gas needed and good wind resistance
- Flexible and can reach tight spaces
Disadvantages:
- Labor-intensive with poor working conditions due to high heat and toxic fumes
- Low efficiency due to frequent rod changes and lower current capacity
Oxy-Acetylene Welding and Cutting
Oxy-acetylene welding, commonly referred to as gas welding, uses a flame produced by burning acetylene (generated from calcium carbide and water) in pure oxygen. The chemical reaction:
C₂H₂ + O₂ → CO₂ + H₂O + heat
This produces temperatures above 3,000°C, hot enough to melt steel. Oxy-acetylene is widely used for cutting and welding metals, especially on construction sites.
To prevent oxidation during welding, oxygen input is carefully controlled to create a reducing flame rich in carbon monoxide and hydrogen, which shields the weld from contamination. This ensures high weld quality without oxidized inclusions.
Which Is Harder to Learn: TIG, MIG, or Stick Welding?
These three welding techniques are among the most common, each with varying levels of difficulty, applications, and skill requirements.
Stick Welding: The Most Challenging
Stick welding is considered the hardest to master due to the flux-coated rod. Beginners must learn to distinguish between the molten metal and the flux, which takes both visual skill and experience. Managing arc length is another challenge—too short causes sticking, while too long degrades the weld quality. Mastery requires significant practice and patience, often under harsh conditions involving heat and toxic fumes.
MIG Welding: The Most Beginner-Friendly
MIG welding is comparatively easy to learn. With an open arc and visible molten pool, it allows beginners to clearly see the welding process. There’s no need to distinguish flux from weld metal, and the wire feed is continuous. Once voltage and current settings are dialed in, learners can focus directly on torch technique. MIG welding also has high productivity and is widely used in manufacturing, making it easier for welders to find employment.
TIG Welding: Precision Requires Coordination
TIG welding requires fine coordination—one hand holds the torch, the other feeds the filler wire. The distance between the tungsten electrode and filler rod must be precisely maintained, often within 1–2 mm. Touching the tungsten can ruin the weld, making TIG particularly demanding. Its precision makes it suitable for aerospace, medical devices, and pipe welding, but its learning curve is steep—second only to stick welding in complexity.
About Jinhong Gas
As a leading industrial gas supplier, Jinhong Gas provides high-purity gases, specialty gas mixtures, and welding gases such as argon, CO₂, oxygen, and acetylene, which are essential for various welding processes including TIG, MIG, stick, and oxy-acetylene welding. With decades of experience, Jinhong Gas ensures reliable supply, precise gas compositions, and professional technical support to help manufacturers, construction sites, and welders achieve the best results. Whether you require small gas cylinders or large-scale industrial deliveries, Jinhong Gas is your trusted partner in welding and metal fabrication.